本シリーズでは、弊社コムスクエアの熱いモノづくりについてご紹介しております。
弊社では、LED監視の自動化プロジェクトを推進しておりました。しかしプロジェクトの成功には、乗り越えなくてはならない困難な壁がいくつも立ちはだかりました。
前回の記事では、プロジェクトの成功を阻む壁の内、LEDランプを監視するために必要であるセンサーを固定するためのパーツ作りについてご紹介致しました。
弊社が生み出した「どんな場所でも簡単に取り付けられるSmartパーツ」が、できるまでの試行錯誤を詳しく知りたい方は、以下URLからご覧ください。
目次
未知な領域だったLED監視基盤作り
今回はプロジェクトの基本方針であった、従来製品より安価な製品に仕上げるためのポイントとなった「電子回路の基板作り」「機械学習の組み込み」を一体どのように実現したのかをご紹介致します。
その前に電子回路の基盤とは、一体何なのかという所からご説明いたします。
LED監視の「電子回路基盤」
電子回路基板とはプリント基板とも言われ、JPCA(一般社団法人日本電子回路工業会)によると以下のように定義されています。
回路設計に基づいて、部品端子間を接続するために導体パターンを絶縁基板の、おもて面またはうら面とその内部に形成された板の、製品名の総称をいう。有機系絶縁材料では、リジッド基板およびフレキシブル基板がある。また、無機系絶縁材料では、セラミックス基板・ガラス基板・シリコン基板がある。
https://jpca.jp/electron_circuit/
具体的に電子回路基板によって何ができるのかというと、LEDセンサーから得た情報を集積、計算し、その結果をサーバに送信することが可能となります。
そんな電子回路基板ですが、実は弊社内製で回路図を全て起こしました。しかしプロジェクト当初、弊社内で回路図を起こした経験のある社員は一人もおらず、全く知見のない状態でのスタートでした。
普通に考えれば、専門外の領域ですので外部に委託する選択肢もあった中で、一体なぜ知見のない分野に取り組むことになったのでしょうか?
LED監視、未開拓な領域への挑戦
もちろん、当初は電子回路基板作りを外部に委託する予定でした。元々、専門外の領域であったため弊社で作ることを想定していませんでした。
そのため、弊社の社員3名(事業部長、開発部長、開発担当)で、基盤屋を数軒回りましたが、結果、分かったのは、委託すると想定以上のコストがかかるということでした。
LED監視の自動化プロジェクトで目指していた一つの目標として、「低コスト」での実現がありましたが、外部に委託すると何百万単位での費用が発生することがわかり、低コストでの実現から遠ざかってしまうという問題にぶつかりました。
それならばということで、無茶を承知で弊社の開発担当に、知識を吸収しながら基盤作りにチャレンジしてもらうことになりました。
当時のことを彼は以下のように話しています。
『電子回路の基盤作りが一番不安でした。なぜなら、自分自身の知見が薄い分野だったからです。昔、組み込み系の会社にいたのですが、ソフトウェア周りのことをしており、脇で話を聞いていたくらいでしたので。。』
彼は知見は全くなかったものの、知識を吸収しながら製品設計を行い、未知な領域での製品開発を着実に進めていきました。そんな彼の「着実に進めていく姿勢」により、自社内での電子回路基板の開発は成功に至りました。
LED監視、低スペックなマイコンへの機械学習の組み込み
基盤作りに成功した後、次にLEDセンサーから得た情報を処理するための機械学習を組み込む段階に入りました。
当初、データセンターやMSP事業者向けに行った事前アンケートで、閾値の設定やチューニングが面倒だと伺っていました。そこで人の手からAIへと移行できるように、機械学習の組み込みを開始しました。
この段階での作業は、かなり難航しました。
機械学習の組み込みは、従来製品ではよく「ハイスペックなオンプレミスの機器」を用意し、何万件のデータをそのまま解析することで分類し、アラートを出すことが一般的です。
しかし今回のプロジェクトの場合、コストを抑えるため「最低限のスペックをもつマイコン」でデータを処理するということを前提に置いていました。
しかし、用意したスペックのマイコンではメモリ容量や処理容量が少なく、精度の高い機械学習を組み込むことができず、頭を悩ませていました。
そこでマイコンだけに固執するのではなく、AWSのlambdaを用いることで処理容量を増やす工夫を行いました。Lmabdaが選ばれた理由は、インスタンスをゼロから構築する必要がない点です。顧客目線で、いかに負担をかけずに利用してもらえるかを考えた末の決断でした。
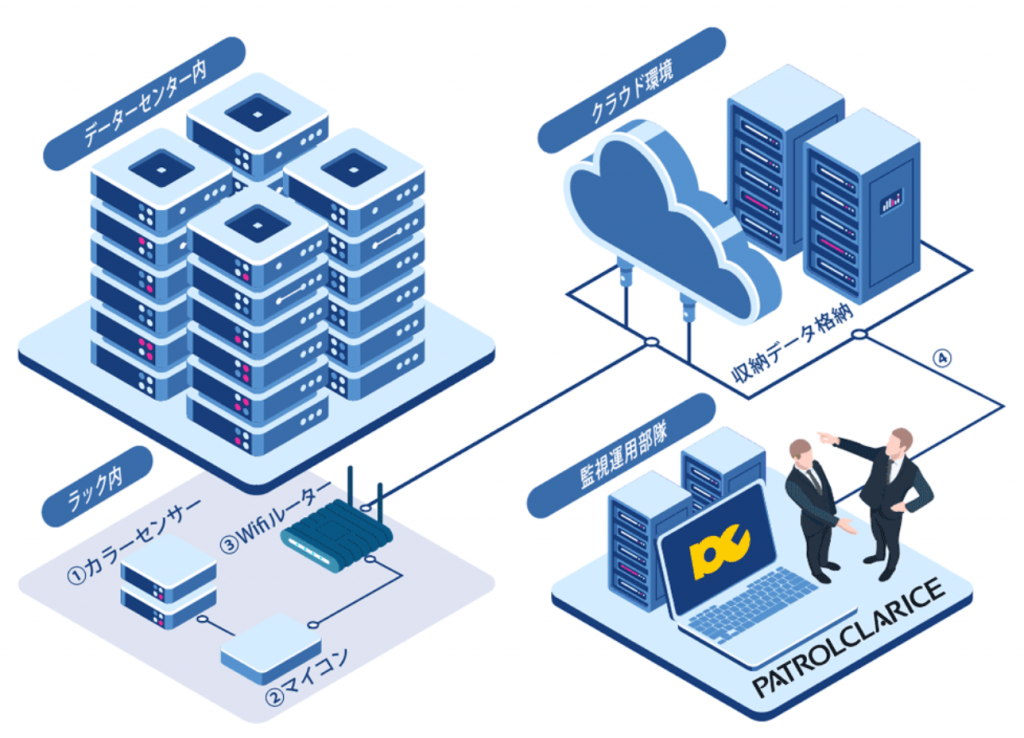
これにより、精度の高いアラートを発砲することができるようになり、製品化の最終段階に進むことができるようになりました。
LED監視プロジェクトを成功に導いたのは
さて、ここまで製品開発における弊社内での試行錯誤をご案内してまいりましたが、低価格かつ使いやすいといった製品コンセプトを前提に、専門外の領域での製品開発を行い、製品化までたどり着いた一番の要因はなんだったのでしょうか?
それは開発担当の「トライ&エラーの速さ」です。
成功の形が見えない中で、トライ&エラーが速いことは、先が見えないプロジェクトの不安を最小化し、かつ正しい方向性をもたらしてくれました。
開発部長は製品リリースを終えた後に、以下のように話してくれました。
『今回はコムスクエアのコアな技術とは無関係なプロジェクトでした。その上、一度失敗していることもあり、かなり不安でした。不安を取り除き、かつ難航するプロジェクトが成功できた一番の要因は、開発担当の彼の「トライ&エラーの速さ」です。今回のような知見の薄い分野での開発は、まさに彼が適している分野で、彼よりトライ&エラーが遅い方が担当していればまた違った未来になっていたと思います。』
失敗を恐れることなく、突き進んだ開発担当の彼のトライ&エラーの速さが、未開拓の領域であったLED監視自動化プロジェクトという困難を乗り越える大きな要因でした。
次回は試行錯誤の末、完成したパトロールクラリス for LEDについてご紹介致します。
是非、ご覧ください。